The Hardest Part of Framebuilding?
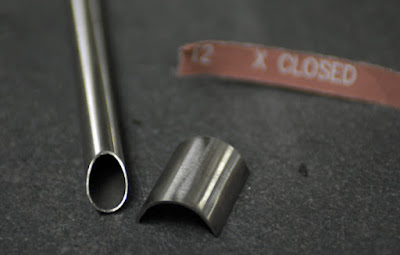
The hardest part is the work. As in, the manual labor.
"If you TIG weld, you will get to sit. I have to stand all day." This was my reply when someone asked which method I recommend learning. She thought I was teasing, but it was an honest reply. Seriously: If you TIG weld, you will get to sit!
What they might not tell you about a brazing torch, is that it is heavy. My first impression of brazing was dominated by this. It is heavy, and yet I had to learn to hold it up and wield it as if it was the lightest thing in the world, for what seemed like an eternity at a time. I was so happy when I finally got used to its heft. But then a week went by when I did not use the torch, and today it was heavy again. It felt like my upper arm, and not the lug, was being lapped at by the flame. (If you TIG weld, you will get to use a tiny little torch, light as a feather. In my dream the welding torch resembled a colibri bird...)
Building this frame is endless work. My hands are a mess. At the end of the day I am drained, unable to do or think about anything else. I just want to go to sleep, and do it again tomorrow. Why? Because hard work feels good if you submit to it. And because building a bicycle frame is fun. And because I'm almost done. For now!
I remember a summer painting program where an instructor said something about painting as a hobby...'it's the best way to paint' ....To do it as work is just plain hard and not for the meek. He was surrounded by dilettantes. I respect those who make things we enjoy and do it year after year after year....it's hard!!
ReplyDeleteFor the painters out there, as far as physical effort framebuilding would be like chopping the wood for your canvas support, putting together the frame, stretching the canvas, boiling your own primer, grinding your own pigment, and then finally painting. Then glazing and sanding it, repeatedly. Except every time you tackle a part of a painting it must be finished within a certain narrow time window or else it will be ruined. Oh and your paintbrush weighs a ton and is on fire :)
DeleteIndeed, the painters I know are like bike builders. Their hands and arms are incredibly strong as they scrap and sand and lift and build and redo an entire 4x6' image in a day and do it again the next day in an attempt to make something which is structurally sound and can exist in the world. Damn hard work!! Not for everyone and all I know encourage others to find some other vocation...something less daunting.
DeleteWhen I was a boy I worked with my uncle the painter (housepainter) and I have ground white lead in oil. And cooked varnish. Don't tell me about the hazards of lead. I've seen it. I can also ride around this city and see work that I did fifty years ago that still looks good. Work my family did one hundred years ago that looks good. Labor well done has rewards
DeleteVelouria, have you tried both brazing and welding? I would be grateful for a serious post about your impressions.
ReplyDeleteI am learning silver and brass brazing (they are different), and I have tried TIG welding. It is not a simple comparison. I do plan to write about it, but am still considering how to approach it.
DeleteGrateful this Thanksgiving, Velouria, and to your readers for this post and all your other posts this past year that share and inspire us with your enthusiasm for cycling and the celebration of its beauty and mystery really. You push us hard to grow with you. You add immeasurably to our enjoyment with your inimitable voice and filter. You have a gift for giving! It's in your DNA. Thank you for being Lovely Bicycle! Jim Duncan
DeleteWelcome to the fold. Building bikes is a heck of a lot of fun, but it is a manual skill based pursuit. I'll agree 100%- the hardest part is the doing. Have fun!
ReplyDeleteThe large majority of humanity works hard every day.
ReplyDeleteYou're doing heavy work when you get home, sit down in a straight chair, immediately fall asleep (before eating anything), and sleep upright in that chair until the sun comes up. Then you arise and do it again.
Amen
DeleteIt is nice to see the intellectuals using their hands and bodies for a change.
ReplyDeleteThen there comes the thinning of the lugs.
ReplyDeleteTime consuming, but not as hard (to me it seems at least) as the dropouts.
DeleteGreat to see girls (of all ages) mowe into the secret world of workshops and tools. Why should the boys have all the fun?
ReplyDeleteDid they tell you what it sounds like when the fire is mowing towards the Acetylene container (the drop it all and run sound)? Just in case you need more to worry about in your dreams..;?)
badmother
"In my dream the welding torch resembled a colibri bird..."
ReplyDeleteFunny that "Colibri" is a brand of cigarette/cigar/pipe lighters (itself a torch, of sorts).
I hadn't thought of how heavy the torch is... not to mention all the hoses, and having to drag them around too.
Yes, the hoses! Making sure not to trip over them too...
DeleteForgot about the colibri lighters, but the association must have been buried in my mind.
I HATE it when people wander into my shop and step on the hoses on my torch or welders, I get all passive aggressive and make an ass of myself. The lines on my water cooled TIG are leaking now and the shroud has a big dirty footprint on it. GGRRRR...
DeleteI could never make a living as a frame builder, my standards of finish run toward "Blacksmith", I like to make sure things are strait and strong but I usually decide it's good enough when it matches the level of finish of, say, your average Raleigh DL1. Great for Bikeracks, scruffy Hot-Rods and the rustic "Mill Furniture" I've filled my house with.
I appreciate perfect bikes and expect the Roadbike I'm having built to be pretty dang flawless, but if I was building it I suppose before it got to the point you're talking about I would have wandered upstairs to the kitchen, made a sandwich and while eating it would just decide to go ahead and throw it together and go for a ride.
Thanks to you and all my other frame building acquaintances(thanks for the encouragement BTW) I'm cutting tubes to build a 29er with 3" tires (ala Crampus) and am considering finishing it with a coat of spray-on car undercoating. No filing and no way to tell if I filet brazed it, TIG-ed it or nailed it together. The guy who's jig I'm using is not impressed but it's just for me, you know.
Spindizzy
Spindizzy, may I humbly suggest doing faux lugs out of either wrinkle finish enamel, or black hammerite? it'll really show off the tubes and contrast favorably with the undercoating...
DeleteI like the idea of a bike called Krampus.
"Ride good all year, or I'll beat you."
Not a bad idea Corey, every toolbox I owned got hosed down with Hammerite when I was a kid and they still look fine a hundred years later, and if black wrinkle was good enough for Ferrari cam covers it ought to be good enough for caveman bikes.
DeleteI really need to finish building a bigger oven so I can powdercoat whole frames, in that case I could just spray on a super thick coat of candy red metalflake and go for the Bassboat look... I keep wondering what would happen if I were to coat the next rack I do for someones DL1 or old Raleigh 3 speed with metalflake instead of the semi-gloss black everyone picks...
Spindizzy
Spindizzy, re: the roadbike you're awaiting--Mercian finish is quite interesting. It's almost vintage in its appearance and unlike anything I've seen on a current production bike. This goes for both frame finishing/construction/dropout style and doubly so for their paint. The story I heard is that this is partly due to Mercian keeping production frozen in time since who knows when.
DeleteThat's part of why I dig their bikes, I just like the time machine vibe of nicely finished but in no way precious. They look hand made by humans instead of the clinical perfection of the very highest state of the current art(which is cool too but not part of my personal fantasy).
DeleteI worried too long about whether to try to make the bike "period correct" for my idea of some golden age of cycling, threaded 1" steerer, skinny tubing etc. but in the end just tried to come up with the most practical modern bike and let the traditional Mercian finish scratch that Brit Bike itch I've got.
I can't wait...
Spindizzy
@MDI
DeleteThe dropout treatment I think you are referring to is a stay-end treatment called dome-and-slot. Reynolds supplied stays and fork blades from the 50s to at least the mid seventies that were already slotted and domed. Almost every English builder bought domed rather than plain. Some tidied up the Reynolds dome a bit and some reworked it and some just put the frames together with stays as supplied. When Reynolds stopped doing that you had to make your own dome by hand. The main tool used was a mallet. Or else you could make your own die. Mercian must have a die. The result is a lot nicer than Reynolds ever made. If you look at older Mercians you'll see stay ends much more like any other English bike.
The Mercian finish is stove enamel. The stove is just a warm closet where the frame is hung to dry. Arranging a warm closet is a spot of bother in the North of England. I'd like to tell you just what the enamel is but the way the trades work is so different in America it would not be understood. It's good enamel and it's so simple to do it can be done at home. Home paint jobs there and then were often pretty good, unlike the botches you can see here in the fixie crowd.
Even when every frame shop did stove enamel Mercian finishes always stood out
"At the end of the day I am drained, unable to do or think about anything else. I just want to go to sleep, and do it again tomorrow. Why? Because hard work feels good if you submit to it."
ReplyDeleteSounds like training. ON the bike.
In some ways. But the main difference is that after training on the bike I feel healthy and vigorous; after this I don't. Being on a bike also comes with an odd sense of glory and glamour that this lacks. If I think of them as drugs, then cycling for me is a stimulant and framebuilding is a depressant.
DeleteEndolphin rush.
DeleteAfter all that interminable work, you'll probably find yourself inexplicably thinking through how to ease the process for the next build, and have a good laugh at your own gluttony for punishment...
ReplyDeleteBoy, do I know the feeling.
For me, the initial big difficulties were learning to properly sharpen a chisel(it took years, really) and how to thickness and join bookmatched plates.
Corey K
I would take some steps back but wouldn't do too many things differently. In fact I think making the same bike over and over, with minor variations, is a good way to improve technique.
DeleteIn my experience the best way to get at all competent at anything is to do the same boring thing over and over again; getting way past the initial learning curve excitement into the long stretches of not even really thinking, but simply doing. Eventually one is able to look back down the hill to discover that all that toil has got you somewhere.
DeleteHey never mind about all that! Everybody scoot on over to Ride Blog to see photo of Peppy in a seriously cute vintage Gazelle cap! Also our very own charming blogeuse in same...
ReplyDeletePeppy aside, the ride blog is worth checking out!
DeleteI would have thought that the hardest part of framebuilding was earning a living doing it...
ReplyDeleteThere is no need to worry about that unless you can, you know, actually do it first!
DeleteGo back and read some of your very first posts on this blog. The contrast - and similarities - are amazing.
ReplyDeleteI hate reading old posts, but I'll take your word for it : ) A lot can happen in 4 years I guess.
DeleteYes. That you can & have moved way past your initial comfort zone (at least at the inception of this blog) illustrates how the inquiring mind will find a way to slake its curiosity and need to be totally absorbed=happy. Your doing this, bending the world of steel with sweat, blood & tears, is the real deal where actual performance can be measured and not just an academic exercise. That you do this despite your damaged hands and no background just shows how important it is that our reach, at least at first, exceeds our grasp. Shows what confidence, intellectual curiosity & a game spirit can do. You've crossed over. Inspiring! Jim Duncan
ReplyDeleteI am a very hands-on DIY person in the real world, which must not come across on the blog given some of the comments I'm getting.
DeleteThe hands thing is, surprisingly, not a problem. It is much easier for me to work on building a frame than to do bike repair & maintenance. I cannot think of any task I've done so far in fact that has required hand strength or digital dexterity. My hands shaking was a problem when I first tried brazing (silver all over the place!) but then I learned to dab the silver at the same rhythm as my hands shaking and it actually works out nicely!
What is the tube in the picture for?
ReplyDeleteIt's a seat stay, with what would soon become a seat stay cap lying next to it.
Deleteyou remind me of the girl in Flashdance
ReplyDeleteAh yes, slotted dropouts. Le bon Dieu est dans le detail. I'm having a bike built that comes standard with plug dropouts, but since I opted for the rest of the bicycle to be filet-brazed, I felt slotted would go with the flow better. So I requested a change, and the builder graciously agreed. It's an upcharge, and because some of the tubing had already been cut I now have to wait until the next batch of frames, but for me it's worth it.
ReplyDeleteBy the way, you can sit and braze...:
http://tinyurl.com/5u7urfe
Of course it helps if you've built a couple hundred bicycles before graduating high school.
My first frame was built with slotted track-ends. Thick hunks of metal, which regrettably meant larger (uglier) diameter seat-stays and brazing with brass, which that presented it's own challenges, not least the matter of getting large hunks of metal up to temperature.
ReplyDeleteI relate to the sense of feeling drained yet invigorated and energised. It's a good kind of fatigue, which doesn't come with a long day behind a desk starring at a computer screen. I too, find frame-building more natural than bike maintenance for some reason. The former feels more effortless.
Incidentally, I can recommend reading Richard Sennett's 'The Craftsman' at a time like this and Michael Polyani's 'Personal Knowledge'. I like how the body comes to tacitly communicate with the materials yet if you were asked to describe your actions to another, you'd be lost for words. This is learning that requires doing, and yet more doing.
Yup, we used brass for the dropouts because of the gaps. Thanks for the book recommendations.
DeleteI would also recommend the book "Shop Class as Soul Craft" by Matt Crawford. He makes the case for how we've largely slipped away from being in touch with our physical world and the satisfaction of manual work because of the pressure to succeed in the world of information exchange.
DeleteSennet? Polanyi? Crawford? I suggest Springsteen - more fun and much more insightful.
DeleteA very big and loud "+1" for Crawford's book. A sign that it is exceptional is that he has an academic background and writes like an academic -- **but still thinks clearly and write clearly**. If that isn't miraculous, I don't know what is.
DeleteI don't agree with everything he says, but he has thought clearly about certain fundamental issues of work, meaning, and identity and made many excellent critiques and some valid conclusions. And he is genuinely funny -- another sign of his intelligence.
Somervillian - Thanks for the book suggestion. I will check it out.
DeleteThomas - each to their own although there's nothing wrong with the Boss.
Here is a link to a folder of images of my first-build, which I'll share here for a week or so before deleting:
https://www.dropbox.com/sh/mw67vxt6smcl26h/GyVfioRp5A
Originally, I intended a 3-speed or Duomatic however I settled on a single-speed. All the tubing is Columbus Life (A shame to give decent tubing to a rank amateur like me - I should've been given some lengths of old pipe and told to go for my life!) and Long Shen lugs.
As you can see, the seat stays aren't terribly pretty but I've received a lot of positive comments while riding and more than a few people have asked about it and asked if I plan to make more. One offered to buy it off me on the spot. I wonder if they'd be so interested if I told them the price they'd have to pay.
Given it was my first build (I'm gradually putting together a workshop), I chose fairly bog-standard, no-name sealed bearing hubs and tektro calipers. Built the wheels - rims are Mavic and spokes are Sapim. Other components are fairly self-explanatory. The colour is RAL 6011, Reseda Green.
One images shows the workshop where I put the bike together. That amazing Aladdin's cave is Den Rustne Eike, or The Rusty Spoke, which is owned by a certain Einar Bowitz who has been collectig bikes and parts for 50 years. He has over 400 Norwegian made bikes in the collection dating from the 1880s to 1990's. The bike above the metal drawers dates from the 1890's for example. And the red and white swanned-necked step through is a 1960's DBS that has only been ridden (briefly) once.
If you want to find unused and boxed Sturmey Archer or Torpedo hubs from the 1950's for example then this is the place. He has shelves of them. He has recently decided to begin assembling these parts into bicycles. I've included a photo Einar with one of his recent creations - the frame is a 1950's Norwegian Diamant. These frames were pegged and dipped whole into molten vats of brass.
If ever you find yourself passing through Oslo, you must drop by Den Rustne Eike. Bear in mind it's only open on Thursday or whenever Einar feels like it!
Good luck with your build Velouria. I'm following your progress with keen interest and with a smidgen of envy. I want to return to the workshop and build another frame and fork!
I forgot to add that some information on my build. 72 degree head and seat tubes, 435 mm long chain stays for a reasonably relaxed yet surprisingly nimble ride. Trail is about 5cm. I've refined the design in RattleCAD based on my experience of riding it and certain aesthetic changes that I'd made and would like to build a new version some day.
DeleteI should say, 435mm from the centre of the bottom-bracket to the centre of the track-ends.
DeleteAgreed, super, I just like playing the anti-intellectual from time to time (actually, all the time!).
DeleteSupermundane, nice work! ? And the shop looks very cozy.
DeleteFor the record, I disagree with some of the points that Crawford makes, and I also disagree with his narrow definition of a "tool" (his definition strictly excludes anything not physically held by hand, so software code built to execute a task could not be considered a tool). However, something really resonated when I read the story of his own career trajectory. I'm also a former academic that got lunged into a career of "information exchange" but don't get nearly the satisfaction from it as I do tinkering with bikes (or home repair, or car repair, or gardening, or doing ANYTHING with my hands). One day I will have to make a drastic decision, and I'm just wondering when that will be.
Going back to Thomas's earlier comment of juxtaposing "the intellectuals" with those "using their hands and bodies," I think it's a huge problem in our society that these are treated as polar opposites. I had the misfortune of being diagnosed as gifted in my youth. This meant that I was actively steered toward a path of academia through most of my education and away from formally learning any concrete skills. This was a terrible thing for me, because I know now that my mind is simply not built academically; I am neither intellectually rigorous nor sufficiently excellent at processing abstract concepts. I did well at university and at my job, but it was mostly through compelling story telling and creativity, and not the actual science/research whatever I was doing. And ultimately I was miserable, it just felt wrong. When I do things that are more physical and concrete - be they photography, painting, or attempting to make useful objects - it just makes so much more sense given how my mind works; I am happier. Had I not gone the academic route, perhaps my real talents, whatever they are, would have been given a chance to surface when I was young enough for it to matter. Youngsters be warned!
DeleteThanks Somervillian. I probably didn't put anywhere near the amount of research that Velouria appears to have into her build before jumping in - research into frame geometry, material properties et al before commencing. I tend to be the kind of person who needs to learn through doing.
DeleteAs to the geometry I ultimately settled on an amalgam of things I've liked in other bikes over the years and actually changes were made on the fly during the build. Perhaps not the most ideal way to approach things but what resulted however was a better ride than I could have expected given the approach - the tubing feels right for me - the right balance of stiffness and flex and despite the potted roads of Oslo and the fact that I'm running on 28mm Eno Cicli Grande Compes, the ride isn't harsh. There's surprisingly very little 'chatter' through the frame.
What does need to change at the very least is the gearing - 48x16 is just too high for the hills of Oslo, and it certainly makes it feel heavier on hills and from a start than it really is (around 9kg or 19lb). It certainly keeps me fit. I'll try an 18 and 20 tooth freewheels and see how it goes.
The next build will certainly employ better components all round but given there are a litany of errors and sins beneath the paintwork I simply wanted to build a bike that I could ride without being too precious about it; that I could ride, enjoy and learn from. So far it hasn't collapsed beneath me.
As to what constitutes a tool, Sennett is quite clear that software is considered a tool when employed with the ethos of a Craft-person, which he sets out to describe. It is that which dignifies us rather than dominate or usurp, transforming the human into an appendage of the machine.
Thomas - there's nothing anti-intellectual about the Boss. Now if you've suggested say Rihanna?! In any case there's no one right way to experience.
Velouria - your experiences sound quite similar to mine. I'm happier creating - engaged in that almost absorbing syncroncity between hand, mind and object. To get all intellual again, a phemonologist philosopher such as Merleau-Ponty would perhaps contend that there is no real distinction.
supermundane - Thanks so much for sharing about your build and for posting the pictures; that is a nice looking bike. Reseda green powder?
DeleteTo tell the truth, much of the research I put into my frame was just done out of bad habit (the habit to research) and proved to be a waste of time. The funniest thing was the tubing. I struggled and struggled to try and "understand tubing" by reading about it, and was embarrassed when I showed up and still did not really get it. I sheepishly told Mike Flanigan this, and so he simply showed me a bunch of tubing, had me look inside and feel around, feel the weight and circumference of different tubes one after another, and then filled the rest in with diagrams and quick explanations once it was all out in front of me. After that I was able to draw my own diagrams, and explain it in my own words. 15 minute hands-on won over god knows how many wasted hours of reading.
Frame geometry is a little different, in that my understanding of it formed over several years of constant riding, with research done mainly to find explanations for what I liked and didn't like about various bikes. I was slow and terrible at understanding geometry (as evidenced by the many funny posts about it here over the years!), but I do think the stumbling process was ultimately useful.
This Sennet book is sounding more fascinating by the minute. So "intellectuals" can't even craft without arguing about the semantics of being a craftsman? : )
Super, if I may, Bruce Springsteen is intelligent, but he is no intellectual, thank God, and I think he would be the first to say so. I use the word to refer to a certain socio-economic class and tradition (of which I am a part, at least nominally, although I am deeply working class, to use a phrase that is rarely used by the people it ostensibly describes, in origin) that emerged post-Enlightenment, when the arts and sciences were separated. I think it is wonderful that Velouria and others, particularly of the current generation, are in many ways putting the two together again through the maker movement, steam punks, artisan shops and, yes, transportation bicycles, if not for the first time.
DeleteThanks Velouria. I'm reasonably happy with it. I know there are flaws – to lay one completely out on the table for example, in my haste to finish it (I was running out of time in the workshop) I miss-set the bridge about 5mm too low. Stupid mistake that I didn't realise until I went to afix the calipers!
DeleteSome of brazing took some time to clean up with jeweller's files to give neat lug-lines. I would hope that after a dozen or more, frames the clean-up could be minimised and that I can begin to approach the quality of brazing that I've witnessed watching master frame-builders on youtube and vimeo. However, on a positive note, all the brazes all appear to be solid.
I'm hardly gentle with the bike but it's proven very forgiving over the past year. This bike has taught me a great deal and I enjoy riding it immensely. Most people who've tried seem to approve although most complain about how tall the gearing is and some don't approve of the relatively high bottom-bracket (the drop is about 45mm). The gearing is something I really need to change, or at least experiment with some more.
I had a good teacher in the workshop but I had limited time and access to them and consequently most of the theory had to with the correct handling of a torch and the equipment rather than understanding the properties of respective tubing etc.
I do know a frame-builder living near Oslo, who I've considered politely begging to spend some time with in his workshop. I'd pay him of course, however he has a young family and barely get enough time at the moment for his own builds.
As to this build, aesthetically, I'd have preferred perhaps 2 centimetres more on the the top-tube and for the top-tube to be perfectly parallel. The top tube has about a 1 degree slope on it due to the fact that the where I had it built didn't have any 72 degree top lugs at hand, only a 73. I'm not too keen on the fairly crude track-ends either.
Concerning the paint-job, originally I planned to go for RAL7026 'Granite Grey' however at the last minute opted for the Reseda green, which I'm very happy with. what I find surprising is how different it looks under different light - markedly so.
I went for enamel, professionally done at a local paint-workshop. I had considered powder-coating but opted for a enamel in part because I was talked into it. No regrets of course; the paint has been surprisingly resilient and I do prefer the lustre you get from a wet-coat. CONT...
I haven't paid too much attention to the bicycles I've ridden over the years and in the main, they've been old beaters (my dad's old 80's ten-speed, old roadsters, 80's BMX, a chopper and your standard fare hybrids and the like that are found your local sports (or worse, department) store. There were bikes that clearly felt right, or at least preferable to others, and some that have felt very, very wrong (mostly the department store stuff) however I've not tended to consider why beyond the obvious factors.
DeleteIt's only been over the past few years that I've become more conscious of what I'm riding and what the bike is communicating to me. I've also noticed that you become a better rider; a more confident and more intuitive rider when you permit yourself to listen to the bike and when you've acquired a broader palette.
'Bicycle Science' sits on my shelf however I'm no where near as advanced in understanding geometry as you appear to be. For instance, I've not ridden a low-trail 650B 'Randonneur'-style bicycle – the type that you speak so highly of here but it's evident that to understand why something works, and why it works for you, there's a need to be conversant with as broad a broad range of bicycle types as possible. Like you, for me it's been a stumbling process although perhaps I'm still in the stumbling stage.
I hanker to build a workshop, if only I could find a small, affordable space here especially given it'll be a while before I could possibly recoup the cost of rent and the tooling that I still need to buy.
As to Sennett, he is worth reading. I suppose the book spends a great of time covering what constitutes a 'craftsman' through example as he feels it's important to get the semantics right and in the main I believe he makes a compelling case. The book has flaws of course – he does make factual errors or may overstate a case, and he can loose the point occasionally, getting bogged down in irrelevancies and non-sequiturs. Still it's surprisingly easy to read. The book itself almost feels like a metaphor for what constitutes a craftsman – progress in non-linear fashion fraught with the occasional failure and misstep in the process of doing.
Gosh I've written too much. Thomas if you don't mind, I'll reply to your post soon. Thanks to Velouria for this indulgence.
Mind? It wouldn't be Thanksgiving if I wasn't arguing with someone. Thanks, indeed, Velouria, for your indulgence.
DeleteOkay, I've ordered the Sennett book : )
Delete